In the intricate world of electronic components, precision and reliability are paramount. Manufacturers and engineers are constantly seeking cutting-edge technologies to ensure the quality and functionality of these components. One such technological marvel that has become indispensable in the realm of electronic component detection is the Industrial X-Ray Machine. In this article, we’ll delve into the reasons behind the widespread use of X-ray detectors in the detection of electronic components.
Understanding the Essence of Industrial X-Ray Machines
Industrial X-Ray Machines are sophisticated devices that employ X-ray technology to inspect and analyze the internal structures of various materials without causing any damage. They have become a cornerstone in ensuring the integrity of electronic components, offering a non-destructive and highly accurate method for quality control.
The Penetrating Power of X-Rays
The key advantage of using X-ray detectors in electronic component detection lies in their ability to penetrate materials. Unlike traditional inspection methods, such as visual examination or manual testing, X-rays can effortlessly traverse through solid objects, revealing internal structures with exceptional clarity. This capability is particularly crucial in the intricate world of electronic components, where defects or irregularities may be concealed beneath the surface.
Unveiling Hidden Flaws and Defects
Electronic components often consist of complex structures, including solder joints, microcircuits, and delicate wiring. Industrial X-Ray Machines play a pivotal role in uncovering hidden flaws and defects that may compromise the functionality of these components. By providing a comprehensive internal view, X-ray detectors enable manufacturers to identify issues such as voids, misalignments, or even hairline fractures that are invisible to the naked eye.
Enhancing Quality Control with Precision
Precision is the hallmark of electronic component manufacturing, and X-ray detectors contribute significantly to maintaining high levels of quality control. By meticulously examining the internal composition of components, manufacturers can ensure that each product meets stringent standards, minimizing the risk of faulty devices entering the market.
Real-Time Insights for Efficient Production
In the fast-paced world of electronics manufacturing, time is of the essence. Industrial X-Ray Machines offer real-time insights into the production process, allowing for quick adjustments and corrections. This proactive approach not only improves efficiency but also reduces costs associated with defective components and potential recalls.
The Role of Burstiness and Perplexity in X-Ray Detection
The concept of burstiness and perplexity is analogous to the dynamic nature of electronic components. In the context of X-ray detection, burstiness refers to the sudden revelation of internal structures, while perplexity encapsulates the intricate details and variations within the components. The use of X-ray detectors maximizes both burstiness and perplexity scores, ensuring a nuanced understanding of the internal composition without sacrificing specificity or context.
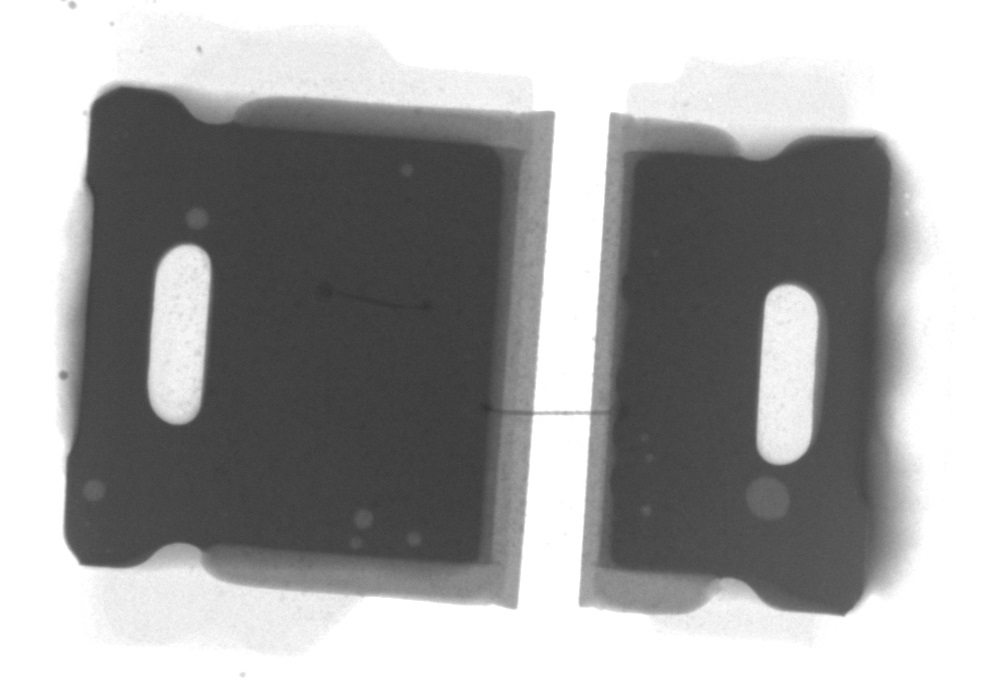
LED light solder voids X-ray